Resolving Adhesion Problems in Post Die Casting Operations
- Hill and Griffith
- Oct 10, 2014
- 9 min read
Introduction
In the Die Casting Industry, many of the castings manufactured undergo secondary operations incorporating the use of paints, adhesives and other polymers such as RTV (Room Temperature Vulcanization). The application of these types of materials requires the polymer to bond to the metal substrate (surface) of the casting. When this bond fails, it is considered to be an adhesion problem. For the die caster, this can be a very costly problem; therefore, it is imperative that it be solved quickly.
To gain a better understanding of the problem and its potential solution, the following points will be discussed.
What creates Adhesion?
What prevents Adhesion?
Assessing the Problem
Solving the Problem
Please note: For the purpose of this paper, it will be assumed that all of the coatings and polymers along with their curing processes are performing without problems.
What creates Adhesion?
It is generally agreed that the primary forces creating the adhesion phenomena are chemical bonds and mechanical interlocking.
Chemical Bonds
An Ionic Bond is a chemical bond formed by the electron attraction between positive and negative ions. An example of this type of bond is NaCl or table salt, where the Na+ (Sodium) ion carries a positive charge and the Cl- (Chloride) ion carries a negative charge.
Van der Waals bonds are forces that result from the interaction of the positive and negative charges between neighboring atoms or molecules. These bonds exhibit themselves in very long chain molecules that make up polymers that are part of our everyday life, such as rubber and plastics.
Although the strength of the Van der Waals bonds is fairly weak, collectively, they represent a significant force within the adhesion bond.
While it is not known which type of chemical bonding is predominate, it is known that a combination of both Van der Waals and Ionic bonding takes place between specific components of the polymer (coating) and the reactive hydroxyl groups/metallic ions that form on the surface of the metallic castings, particularly aluminum alloys.
Mechanical Interlocking
With Mechanical Interlocking, good adhesion only occurs when the coating/polymer penetrates into the pores, holes and crevices and other irregularities of the surface of the casting, and locks mechanically to it after curing. The coating/polymer must not only wet the substrate, but also have the right rheological properties to flow into the pores and openings in a reasonable time before the curing process begins to take place. See Figure 1.1.
What Prevents Adhesion?

Figure 1.1 - Graphic illustrating surface irregularities

Figure 1.2 - Surface contaminants inhibit or prevent proper adhesion
Any material, organic or inorganic, or process that prevents the polymer from having intimate interfacial contact with the metallic substrate will inhibit or prevent the adhesive bond from forming. This could be surface contaminants, such as dirt, wax, oils, moisture and excessive oxide layers. See Figure 2.
Assessing the Problem
There are several steps in assessing the specific adhesion problem.
The first step is to determine the chemical make up and physical nature of any contaminants present on the surfaces of the castings where adhesion failed to take place. This can be accomplished through Analytical Chemical Testing.
There are two specific types of analysis that are crucial to the identification of the source of the contaminants; Fourier Transform Infrared Spectroscopy and Energy Dispersive X-ray Spectroscopy:
Fourier Transform Infrared Spectroscopy (FTIR)
This kind of Spectroscopy identifies chemical bonds in a sample by exposing the it to an infrared laser and recording the different wavelengths at which various chemical bonds absorb, thereby producing an infrared absorption / transmission spectrum. The resulting spectrum produces a profile of the sample, a distinctive molecular fingerprint that can be used to easily scan samples for many different components. See Figure 1.3.
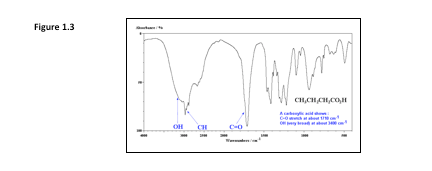
Figure 1.3 - A profile of a sample
Energy-Dispersive X-ray Spectroscopy
Energy-dispersive X-ray spectroscopy (EDS, EDX, or XEDS) is an analytical technique used for the elemental analysis and chemical characterization of a sample. It relies on the interaction of a source of X-ray excitation and the sample being evaluated. Its characterization capabilities are due to the fundamental principle that each element has a unique atomic structure allowing unique set of peaks on its X-ray spectrum. Refer to Figure 1.4

Figure 1.4 - Energy-dispersive X-ray spectroscopy
The data from these two analyses will provide the die caster with sufficient chemical information to identify the source or sources of the contaminant(s) responsible for interfering with the adhesion bond.
The second step is to identify which of the products that come in contact with the casting could be the source(s) of the contaminant(s). The chemical characterization of the contaminant(s) should very helpful in narrowing down the search. For instance, die release agents can contain wax and siloxane components and their presence is easily detected through the FTIR analysis. While excessive an amount of aluminum hydroxide is detected through the EDS analysis.
Following is a list of possible sources of contaminants: Table 1.1
Die Lubricants
Trim Lubricants
Plunger Lubricants
Machining Fluids
Quench Solutions
Wheelabrator Media
Storage Materials / Cardboard or Plastic
Atmospheric Soil
Each of these should be evaluated as possible contributors to the problem.
The third step is to evaluate the pretreatment process.
The pretreatment process is a system designed to remove contaminants, modify the casting surface to be adhesion friendly, and seal the surface for protection against corrosion. Although, there are several different designs of pretreatment systems, the most effective systems incorporate 5 stages or more. See Figure 1.5.

Figure 1.5 - The most effective systems incorporate five or more stages
All of the possible sources of the contaminants listed above come in contact with the casting before it is submitted to the pretreatment process. If there is organic / inorganic contaminant(s) remaining, then the pretreatment system is either not working effectively or it is incapable to address the full range of contaminant(s) being introduced to the system.
Evaluating the Pretreatment Process
Chemistry
Cleaner
The most popular and most used aqueous cleaners used today are the high alkaline cleaners (pH >10.0). Although they are very effective against stubborn soils, most of the alloys used in the casting process (aluminum, zinc and magnesium) are attacked by these high alkaline cleaners and often create a process called smutting. Smutting is where the Caustic of the Cleaner reacts with the surface of the metal forming a layer of metallic oxides and hydroxides on the surface of the casting. This condition is detrimental to adhesion.
Therefore, mild alkaline cleaners containing inhibitors are usually the product of choice.
Concentration of the cleaner should be checked at least 2 times a shift to make sure that it is within the process specifications. Also, system should be periodically dumped and recharged to eliminate excessive build up of soils.
Conversion Coating
Once a casting has gone through the cleaner stage and been rinsed it is subjected to an acid bath of some type to remove any oxides on the surfaces that may have formed in storage or transportation.
Often an Iron Phosphate Treatment is used to etch the surface of the alloys as well put on a conversion coating in preparation of the polymer. While this is effective when preparing steel parts to be coated; with aluminum, the normal acids do not etch the casting and the reaction between the phosphate and aluminum never takes place. Therefore, the majority of the pretreatment processes have incorporated an ammonium bifluoride, which creates a weak solution of hydrofluoric acid. This acid readily etches the aluminum surface creating fresh sites for the Mechanical Interlocking mechanism of adhesion to take place.
The amount of iron phosphate and hydrogen fluoride (when present) should be checked at least once per shift to assure that there is sufficient material to properly etch/coat the surface.
Sealer
After a metal surface receives a conversion coating, the surface is water rinsed to remove unreacted chemicals, and a sealer is usually applied. The sealer increases the corrosion and humidity resistance as compared with conversion coatings without final sealers. In the case of electrocoat applications, final deionized (DI) or reverse osmosis (RO) water rinse is required to minimize contamination of high-conductivity water on the substrate surface from the post rinse. In these cases, it is imperative to have a reactive final rinse that maintains its properties after the DI or RO rinsing rather than a dry-in-place rinse.
Sealers historically have been based on chromic acid, however, with increasingly strict effluent limitations, most finishers have converted to either trivalent-chrome or non-chrome post-treatments.
Water
The chemistry of the water can impact the overall coating process, by leaving hard water deposits on the casting surface. Reverse Osmosis water is the most ideal source of water to be used in the system; however, many finishers’ choose to use either city or well water. In those cases, the Pretreatment Tanks need to be monitored for excessive hard water salts build up at least once per day.
Temperature
A die lubricant’s chemical components (waxes, silicones, oils) are designed to withstand the heat of the die casting process. Therefore it should not be a surprise that heat would be used in the removal process of its decomposition products.
Heat enhances the cleaning by:
Synergistically increasing the chemical activity of the cleaner
The chemical reactivity of a cleaner is directly proportional to increases in temperature. This increase in activity allows the surfactants to penetrate the surface crevices and lift out the contaminants as well as etch the surface in preparation for the coating /polymer.
Please note: It is important to make sure the temperature and chemical concentration are controlled to avoid excessive etching (smutting) especially with aluminum alloys. This smutting can and will cause adhesion problems as well.
Liquefying and emulsifying stubborn contaminants such as waxes or high molecular esters that exist in a solid state when not emulsified.
Low to medium melt point waxes and siloxane (paintable) polymers can sometimes be removed with a mild alkaline cleaner running at temperatures of about 130 - 150º F , however high molecular polyethylene (synthetic) waxes do not begin to soften until a much higher temperature range (160 – 180 º F). These types of waxes require that the casting substrate be heated sufficiently to the point that the wax begins to soften and allows the cleaner’s surfactants to get under the contaminant and lift it to the surface where it can be removed by the washer spray or agitation.
The heat should be held between 160 – 170˚ F. If the temperature is much lower than this, some of the residues will not soften and resist removal.
Pressure
Too many times, people forget that cleaning is not only a chemical process but also a physical one.
Chemical cleaning requires the surfactants to be able to interact with the soils. However due the stubbornness of many soils (high temperature waxes), mechanical energy is required to perform the actual removal of the soil from the substrate. Spraying is a more effective means of removal than immersion or submersing.
The higher the pressure, the more efficient the cleaning process. Recommended pressure is between 15 – 20 psi, but is often determined by the geometry and size of the part. Too high of pressure will result in parts being blown out of their baskets or hangers.
It should also be noted that the spray pattern associated with pressure should be check to make sure that the spray is making proper contact with the part.
Time
You can have all the proper components in the Pretreatment System, but if the process does not allow enough contact time between the part and the treatments, the parts will not be properly cleaned and prepared for the polymer. Also if there is too much time, exposure to the cleaner and conversion coating stages will have adverse effects on metal surface.
Solving the Problem
Once the source of the contaminant(s) has been identified and the pretreatment process has been reviewed, the solution is found in the answers to the following two questions?
Are the process variables in specified ranges?
If the process variables are outside the specified ranges, then the appropriate adjustments need to be made and castings tested after the adjustments to verify that the problem as been resolved.
If process variables were within specified ranges, then what needs to be changed in order to solve the adhesion problem?
Depending on the nature and source of the contaminant, adjustments such as cleaner concentration, temperature, location of spray, and time are all variables within the system that are adjustable. One variable needs to be adjusted at a time and parts evaluated.
There are also some post treatment operations that are being incorporated after pretreatment to assist with the adhesion process;
Post Treatment Alternatives
Baking Ovens
The castings are raised to a temperature of 400 F for periods ranging from 15 minutes to 60 minutes. This is to eliminate any remaining organic contaminants that might create out gassing (raised deformities) or prevent proper adhesion.
Plasma Treatments
Within this process, a plasma field is formed when flammable gas and air are combined and combusted to form an intense blue flame. Brief exposure to the energized particles within the flame affects the distribution and density of electrons on the substrate’s surface and polarizes surface molecules through oxidation. This method also deposits other functional chemical groups that further promote adhesion.
The Flame plasma process generates more heat than other treating processes, but materials treated through this method tend to have a longer shelf-life. These plasma systems are different from air plasma systems because flame plasma occurs when flammable gas and surrounding air are combusted into an intense blue flame. Objects’ surfaces are polarized from the flame plasma affecting the distribution of the surface’s electrons in an oxidation form. (www.plasmatreating.com)
Summary
It is the author’s desire that the information shared in this paper will be helpful to the die caster regarding specific steps to take in troubleshooting and resolving future adhesion problems.
The keys are to know what contaminants are contributing to the adhesion failure and are the pretreatment stage variables operating with the specified limits? Until those two evaluations are performed, all adjustments to the process are shots in the dark.
About the Author
Tim Cowell is the Technical Director for The Hill and Griffith Company. He has over 28 years of experience in the Metalworking Industry. He is responsible for new product development, working with die casting and machining manufacturers on special projects and providing technical support to the technical and sales teams.
Tim has a BS degree in Chemistry from Cedarville University. He has authored several articles on paint adhesion problems, die casting continuous improvement initiatives and scrap reduction projects. Tim also assists as an instructor for several North American Die Casting Association courses.
Comments