Reduce Die Casting Cracks by Proper Use of Lubricants
- Hill and Griffith
- Aug 23, 2017
- 2 min read
NADCA EC-515 Die Casting Defects Course Review, Basics for controlling die casting defects - By Dr. Steve Midson
Reduce Die Casting Cracks, or tears, or hot cracks have many causes, but usually are at least partially caused by shrinkage cracks on the surface
Most often, the casting is stretched in the die as it cools because the die doesn’t change dimensions while the casting is cooling and contracting. The stretching causes cracks at the weak point (the last point to solidify)
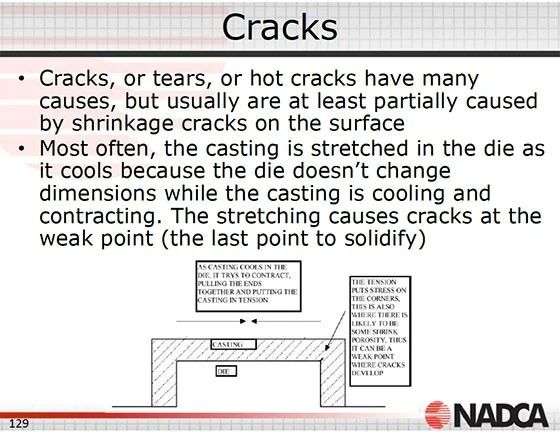
Shrinkage cracks on the surface occur during solidification, and have a dark surface - cool the corners or heat up the adjacent areas, add radii to the corners for this type of crack
For castings that crack while cooling in the die, the crack will also be at a hot spot – increase radii
Mechanical stress can cause cracks when the die opens or the casting ejects (or during slide operations)
Cracks at the base of long cores or fins, dragging or sticking of projections into one die half may indicate die shift when the dies separate
The factors in die alignment should be checked, such as: die “droop” (no die carrier), worn guide pins, worn linkage, worn tie bar bushings, worn shoes under the moving platen, uneven tie bar stress, etc.
The cracks at ejection are usually accompanied by drag marks of some sort.
Check the ejector plate for worn bushings, be sure the ejector plate operates straight. Look for undercuts from erosion in the die that cause the casting to hang up

(Thanks to All About Metallurgy for posting this PDF. We'll cover other aspects of die casting defect control by the proper use of die casting lubricants from the course in upcoming blog posts)
(If you liked this article you might also like this post on, "Die Casting Defects")
Comments