Green Sand Metalcasting - 3D Printing as an Alternative to Patternmaking
- Hill and Griffith
- Nov 29, 2016
- 6 min read
(This post highlights some more of the new capabilities of 3D printed cores. The article is from ADDITIVE MANUFACTURING, 1/20/2014, Peter Zelinski, Editor-in-Chief, Modern Machine Shop)
Hoosier Pattern has changed its business in a way that dramatically expands the design freedom available to its customers. Historically, the company has machined foundry patterns. Today, it uses 3D printing to create molds and cores directly from sand.

Because of the undercut, this core would be challenging at best to produce using a core box. 3D printing opens the door to geometric freedom such as this. Another interesting detail about 3D printing: It can produce the part’s own packaging. Inside this box is a core that might have been too delicate to ship. Hoosier Pattern therefore printed the box around it, which the customer can cut away after the part has safely arrived.

A core is a production part. Because each core is used one time, it is produced in production quantities. Accommodating order quantities is a basic change the pattern supplier had to make.

The 3D sand printer might run for more than 24 hours in a single cycle, but it is making numerous mold components during that time. Different parts and different customers’ jobs can be nested in the build volume. In fact, because unfused sand supports the parts, jobs can be nested in three dimensions. The document in the foreground is a map of the nesting for the build that has just been completed.

Steve Murray shows a sand mold component that would have required a complex pattern involving inserts to produce the various slots. 3D printing made this component much easier to produce.

The 3D printer builds complex forms in sand by fusing one thin layer after another. The following shot is typical of how many components might be produced in a given cross-section of a given build.
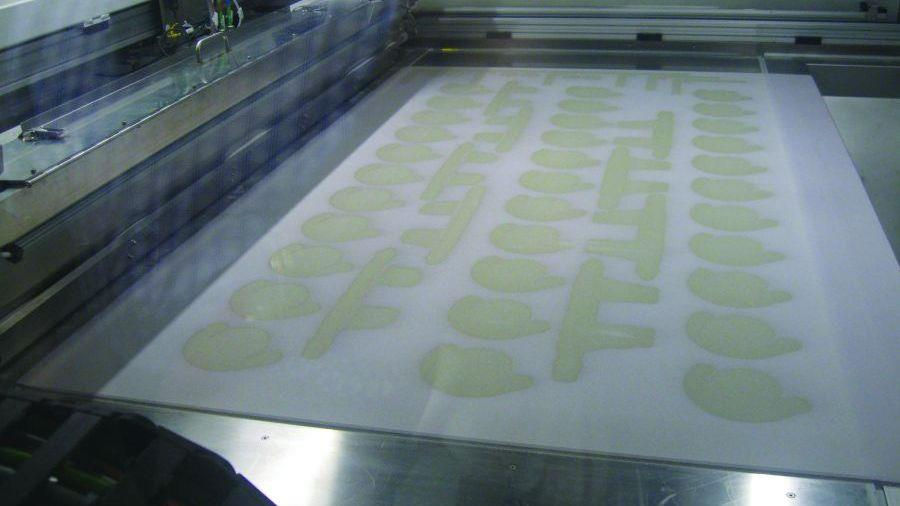

A core is a production part. Because each core is used one time, it is produced in production quantities. Accommodating order quantities is a basic change the pattern supplier had to make.
Steve Murray says the problem with being a pattern supplier is that you often play the role of killjoy.
The salesperson with Hoosier Pattern of Decatur, Ind., is a journeyman patternmaker himself. He talks to customers about the parts they want to produce through casting. In the vast majority of cases, he says, there is some design compromise the customer has to make to accommodate casting’s traditional requirements. An undercut might need to be eliminated, for example. Or, the internal geometry of the part might be too complex, resulting in an overly expensive core. Or, the part might need to be given a greater draft angle to allow the pattern to pull away from the sand mold cleanly. Because of considerations such as these, a customer usually has to cast a part that is at least slightly different from the design that this customer originally envisioned.
Until now. Mr. Murray’s message to customers has now changed. That’s because Hoosier Pattern has changed. In many cases, the company can now let customers cast precisely the parts they want to make. Rather than counseling customers to compromise, Mr. Murray now urges them to try to design the part that is optimal for the application. He often encourages them to look for ways that added complexity might remove unnecessary weight or improve the performance of the cast component. It is almost as if he is now able to say, Don’t worry about the manufacturability.
The reason for this new freedom is 3D printing. Hoosier Pattern recently expanded its capabilities—actually transformed its capabilities—by adding an ExOne S-Max sand printing system. This is a machine that 3D-prints mold components in sand without any need for a pattern or core box. The machine essentially makes sand molds without the middleman.
To established professionals in the foundry industry, this can seem weird. Pattern shops supply patterns and foundries pack sand around them to make the mold—that’s the way the industry works. For the pattern shop to skip the pattern and instead supply the sand mold is a change that Hoosier Pattern’s customers sometimes have had to pause to wrap their heads around.
However, this change both simplifies the casting process and overcomes many of its previous limitations. 3D printing of sand potentially makes casting both more efficient and more effective at the same time.
A pattern shop is a machine shop. Hoosier Pattern has around 30 CNC machine tools. For this reason, this company’s introduction of 3D printing is interesting not just because of its implications for casting, but also because of what it illustrates about 3D printing. As Hoosier Pattern’s example shows, 3D printing, or additive manufacturing, does not fit neatly into established manufacturing categories. That is, it does not directly take the place of processes such as CNC machining or conventional patternmaking, largely because its successes come from enabling parts that these conventional processes could not have produced. Rather than competing with any one existing process, additive manufacturing does something larger: It collapses the overall sequence of processes, and it rewrites many of the established manufacturing rules.
Straight to Sand
A primer on casting: A casting is a molded part for which the mold is often made of sand. This mold is created by packing the sand around a pattern. While the mold is a negative of the cast part, the pattern is a negative of this mold. Therefore, the pattern—a negative of a negative—is a direct geometric model of the final component.
Empty spaces within the casting (for example, a passage through the cast part) have to be defined by solid sand. The sand tooling that does this is the core, another mold component. To create the core, the pattern shop supplies a machined mold into which the sand is packed—a core box.
Mr. Murray says cores are the real promise of 3D sand printing. CNC machining of a pattern often is not difficult. However, the core tends to be where the real complexity lies and where the most challenging design compromises often have to be made. A complex and critical casting such as an aircraft fuel pump component can require an intricate core box. In fact, the design might necessitate a challenging puzzle of core components that has to be skillfully assembled at the foundry. And because a sand mold is used one time, this assembly is done again and again. That is why the prospect of going straight to sand by creating cores through 3D printing potentially promises not only design freedom, but also significant labor savings.
The technology’s primary drawback is speed, Mr. Murray says. Relative to making a mold off of a pattern, 3D printing is slow. Thus, sand printing usually is not an effective choice for high-volume casting jobs. For these, making patterns and core boxes is the efficient option.
Yet even in these cases, he says, 3D printing can add value as a means of improving the design before the pattern and core machining begins. The customer can use sand printing to cast different versions of the design, testing various actual castings in their end use before a final design is committed to production. This prototyping, like high-complexity jobs and low-volume jobs, is another of the cases in which sand printing makes sense.
One other case is when the material cost is high, or when merely the cost of the part weight is high. In aircraft manufacturing, the need for draft angle can be expensive, because that angle constitutes added material and therefore added weight. However, the draft is only there because of the pattern. Doing away with the pattern eliminates the need for the draft angle, meaning sand printing might be an attractive option in this application even if the part quantity is high.
Impact on Machining
That need to account for part quantity was actually one of the most fundamental challenges Hoosier Pattern confronted when it began to consider acquiring 3D sand printing, Mr. Murray says. A pattern is a unique part, so Hoosier Pattern had built its business on one-off manufacturing. Getting into the business of creating sand molds meant that its ordering and tracking process would now have to allow for batches of parts—a dimensionality to its production that hadn’t been there before.
This difference, among others, made sand printing distinct enough to merit giving the sand printer its own staffing and its own room within the facility. Now busy enough that it runs almost continuously, the ExOne system comprises what is essentially a sand mold factory within this patternmaking company. Customer orders that might have required patterns in the past are instead fulfilled in this room through an entirely different approach to running the job.
But that doesn’t mean the machine shop is slowing down. Mr. Murray says machining capacity is likely to expand, because this new capability is also spurring activity within the established shop. The freedom to create molds for complex castings gets Hoosier Pattern in the door with customers it might have never had the chance to serve before, he explains. When this happens, the resulting relationship often leads to conventional pattern machining work as well.
Comentários