Review of Reliance Foundry's, "How to make green sand for metal casting foundry" article
- Hill and Griffith
- Jan 15, 2019
- 5 min read
This is a great basic description of the "Green Sand" foundry method.
"Molding sand is at the heart of the sand casting process. It must hold a shape well and capture the fine details of a casting, yet be permeable enough to allow gases to escape. Under the strain of having the molding pattern removed from it, or while it is filled, it cannot crumble or sink on itself. When it is turned upside down it must not lose its form: the parts of a mold have to stay true while clamped together. In most cases, “green” sand is enough to evidence these properties. Green sand is not called that because of its color—these materials can be a wide range of colors depending on composition and use. Instead, it gets its name because it is damp, like green wood.
Sand permeability is the “venting power” of the material—how much gas it will allow to escape the mold. Green compressive strength captures how much compression the sand can handle before it begins to crumble. Green shear strength measures the strength against structural failure under shear stress: this is a force that produces sliding failure parallel to its direction. Sands are also tested for their dry strength, for they will generally lose moisture in the process of filling. Hot strength (behavior at elevated temperatures) is also checked. Will the high heat of casting cause the mold to crumble? The special mix that creates foundry sand provides the needed behavior. The main ingredient is a mineral sand with a consistent grain size. The size of the sand’s grain will affect the finish of the casting, but also sometimes the permeability and porousness of the mold. This ingredient alone is not enough: a bonding material, usually clay, is added, and the blend is moistened with water. There are a number of options available to a foundry when mixing a recipe for sand casting. Mineral sands The mixture at foundries is usually 75-85% sand, with the rest being clay, water, and other additives. The sand can be found naturally, usually from a lake, or can be created after mining and standardizing clay free minerals.

Olivine Traditionally, an olivine sand was used for metal casting in both ferrous and non-ferrous foundries. This sand could produce a fine finish by cooling the metal rapidly, and it made for a very low dust environment that is not dangerous to breathe. It was considered a “forgiving” foundry sand, taking patterns well and not expanding when hot, but its tensile strength is not very high. Silica sands have always been preferred for cores. Some olivine sands would have a very light green tinge, but that is a coincidence—like everything else, it can come either “dry” or “green.”
Olivine sand does not have the tensile strength of silica but produces no harmful dust. Olivine sands are no longer mined in the United States so, at least in North America, this is no longer the primary source of foundry sand.

Silica Ferrous foundries (those dealing with iron and steel) usually use silica sand, sometimes known as quartz sand. Silica sand has long been used in core making, so switching to using the same aggregate throughout the casting process has made the process of managing foundry supplies easier.
Silica sand is the most commonly used type of foundry sand. Foundries using this product take some additional minor precautions against silicosis, which is a disease that can form in the lungs of those who have breathed in a lot of silica particles. Sometimes respirators or filtration masks are used.
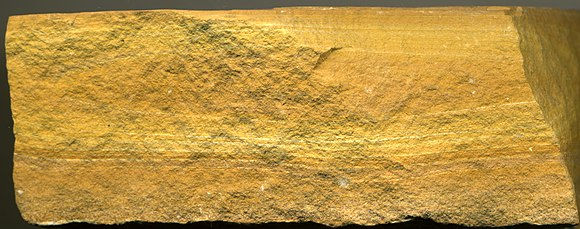
Clay in green sand Green sand is usually 10% bentonite clay. On a molecular level, this clay contains an absorbent mixture of silica and aluminum, and commonly also has potassium, sodium, or calcium. Calcium bentonite is the most commonly used clay in the green casting process. Bentonite clay is mined and cleaned before being used in a variety of applications. Although it has many manufacturing and building uses, the most common consumer uses of bentonite are in kitty litter and cosmetic products like face masks, where it is used for its absorbent properties.
Clumping kitty litter is a common household use of the bentonite clay used by foundries.
Other additives for green sand casting
Moisture is an important component in all green sand casting. Water is generally added at 2-5% of the weight of the mixture. The hydrostatic bonds between water molecules strengthen the sand: it is these bonds that build sandcastles from wet sand on the beach, and the same forces are at work in the foundry. It is the water that increases the green sand’s capacity to handle shear stress and compression. Special additives may be used in addition to the basic sand, clay, and water. These include cereals, ground pitch, sea coal, gilsonite, fuel oil, wood flour, silica flour, iron oxide, pearlite, molasses, dextrin, and proprietary materials. These all serve the purpose of altering specific properties of the sand to give desired results. Facing sands, for giving better surface to the casting, are used for gray iron, malleable iron, steel, and magnesium castings. The iron sands usually contain sea coal, a finely ground coal which keeps the sand from adhering to the casting by generating a gas film when in contact with hot metal. For foundries using sea coal in all their sands, the mixture runs about 5% coal dust. Gilsonite serves the same purpose, in that it produces gasses to prevent sand sticking or nitrogen related pinholes. Steel facings may contain silica flour or other very fine highly refractory material to form a dense surface which the metal cannot readily penetrate. Olivine sand was also used for castings with manganese steel, as the combination of olivine sand and manganese provided a good finish.

Mold washes are coatings applied to the mold or core surface to improve the finish of the casting. They are applied either wet or dry. The usual practice is to brush or spray the wet mold washes and to brush or rub on the dry ones. Graphite or silica flour mixed with clay and molasses water is frequently used. The washes are usually mixed with water-base or alcohol-base solvent solutions. Alcohol-based solutions might be lit with a flame, igniting the alcohol and instantly curing the mold. Water-based solutions require oven drying time, during which the wash sets and the excess moisture is removed.
Read the entire article, thanks to Reliance Foundry's website.
Green Sand Metal Foundry Related News:
Comentarios