Feeling Out Green Sand Conditioning
- Hill and Griffith
- Oct 10, 2017
- 6 min read
This article looks at the characteristics metalcasters should be looking for in their sand systems.
Explained within is the role additives play in creating ideal molding sand characteristics.
For many metalcasters, there is no substitute for the smooth and silky feel of perfect green sand conditioning. While there have been many improvements in sand conditioning practices to achieve this feel, tests designed to determine ideal sand characteristics remain sub-jective, causing foundries to rely somewhat on guesswork.

The only true way of determining acceptable molding sand lies in the quality of the casting it produces. But for efficient production, the sand must be tested before it reaches that point. As a result, many sand operators return to the old, reliable method of going by feel. The key for foundries is to combine the scientific tests with the unscientific feel to cover both sides and ensure quality sand.
Hooked on a Feeling
First and foremost, a molding sand operator should be looking for a smooth and silky feel. If a metalcasting facility properly aerates its molding sand (from a mechanical source), the sand will have the desired feel. This same characteristic also can be accomplished by increasing the levels of Western (Sodium) Bentonite and chemical modifiers in the sand. Metalcasting facilities that have altered their operations to accommodate these changes have produced molding sand that feels as if it has been aerated before it actually passes through the mechanical aeration.
Another popular characteristic of the desired sand feel is the ability to squeeze a handful of green sand and achieve the desired compaction. This is one of the most popular tests conducted by molding sand operators. The ratio of molding sand compactability to moisture content can be related to the sand compaction characteristic measured by hand.
As a rule of thumb, optimum sand conditioning can be realized when the ratio of molding sand compactability to moisture content is between 10.5:1 and 12:1 in iron foundries (the ratio cannot be applied to other materials). The reason this ratio is preferred to the understanding of sand feel is because molding sand conditioning depends on the balance of active bonding materials (clays) and the addition of water.
In order to thoroughly understand the importance of balancing active bonding materials and water, an understanding of the available water in the bonding mechanism of the sand system is important. Water is available to molding sand in a number of sources. The most obvious is at the muller or mixer when the molding sand is prepared (often referred to as temper water). The other source of moisture is the water that remains after the sand has completed the molding, pouring, cooling and shakeout processes. A widely accepted guideline is to have a minimum of 0.9% water after the sand has completed shakeout and before any water is added from another source. This is critical because the foundry does not wish to dehydrate the clay bonding mechanism that is directly related to sand conditioning. A molding sand system with the greatest optimized mulling efficiency cannot make up for a dehydrated bonding mechanism. (It is important to note that if the muller is not properly maintained it will have a greater bearing on sand conditioning than any other single characteristic. The application of mulling is best discussed with the manufacturer of the equipment.)
Fortunately, the phenomena of active bonding materials (clays) and the water relationship is not totally affected by the different ratios of Western and Southern (Calcium) Bentonites for the bonding materials that exist in the molding sand. When Western Bentonite is added to the molding sand at the muller, it does require more energy time and/or muller efficiency) than a Southern Bentonite. The first condition is a clay binder system that has been mulled and processed through pouring, cooling and shakeout. The other clay content is added freshly at the muller prior to the pouring, cooling and shakeout processes.

The feel of molding sand also relates to the ability of molding sand operators to have the desired squeeze and correct quantity of sand remaining on their hand after it is returned to the molding sand system. Operators should be looking for a minimum amount of fine material remaining on their hand. If heavy fines remain, it is an indication of a buildup of fines in the system.
There are two popular testing methods in the laboratory that can be related to this characteristic — the AFS 25 micron clay wash and a screen analysis of the molding sand. These laboratory evaluations can act as a measurable test to confirm the visual characteristic of the undesirable quantity of fine material contained on the hand after the molding sand is returned to the system.
Another rule of thumb is that the total quantity determined in the AFS 25 micron clay wash should be 1.5-3% higher than the measured methylene blue clay test. If the number is higher, the sand system has a tendency to leave excessive sand fines in the operator’s hand after the squeeze test has been completed.
Enhancing Sand Conditioning
The introduction of additives to a sand system cannot make up for poor sand conditioning practices and/or limits to the engineering in a metalcasting facility. However, certain additives can optimize the performance characteristics of the molding sand system.
The addition of higher levels of Western Bentonite (and in some bond formulations the addition of chemical modifiers) has resulted in sand systems that achieve improved properties without altering other practices.
Molding sand operators and their supervisors have related the improved sand conditioning through additives to the sand feeling as if it has gone though the mechanical aeration even though it has not. Another observation from molding operators is that the sand feels more flowable. In most molding sand systems, a reduction in variability in the sand properties is observed.

Fig. 1. Shown above are changes seen in molding sand properties when compactability is held constant
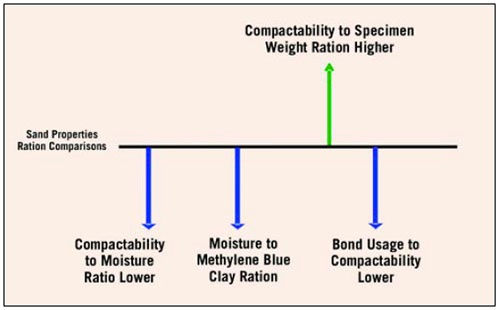
Fig. 2. Shown above are comparisons of sand property ratios.
Figure 1 shares the results of two foundries that have increased the levels of Western Bentonite in their sand systems.
The first operation, which utilizes vertically parted molding and excellent mulling, increased the level of Western Bentonite by about 10%.
The second foundry, which utilizes automatic matchplate molding with proper mulling, upped its levels of Western Bentonite by about 20%. As a result, the foundries increased their sand density and permeability while decreasing the amount of moisture and methylene blue clay required.
The information in Fig. 2 represents observations from the foundries when the sand pro- cess was controlled by holding compactability constant at the muller by using a mechanical sand controller. This resulted in lower ratios of compactability to moisture, moisture to methylene blue and bond usage to compactability. Since most foundries run the molding sand controls based on compactability, the evaluation of sand properties versus compactability was relevant to the understanding of sand control and conditioning.
The information contained in Fig. 2 is a representation of the comparisons of the ratio of physical properties of molding sand and their relationship to sand conditioning. One of the critical comparisons when looking at sand conditioning is the relationship of compactability to moisture. Of equal importance is the consistency of the molding sand between prepared batches. During the six-month investigation period, the increased levels of Western Bentonite and chemical modifiers resulted in a greater level of consistency.
Increasing the levels of Western has an effect on the molding system because foundries prefer high compactability levels. The concept is based on the fact that less water is required to develop compactabilities and lower compactabilities will starve the system for water demand, resulting in slightly more friable sand with better flowability. This also contributes to the lower moisture requirement to develop compactability and the characteristics found in a predominately Western Bentonite bonded sand system.
Examining Your Sand System
The conditioning of molding sand is critical. With the demand for sand performance continuously increasing, the need for a consistent process with superior feel is necessary. The following suggestions provide a framework:
for greater consistency and maximum performance, molding sand should have a compactability to moisture ratio between 10.5:1 to 12:1 in iron foundries
sand must be aerated properly, and while increasing the levels of Western Bentonite and chemical modifiers improves the aeration feel, is not a replacement for mechanical aeration
a build-up in fine materials is usually counter productive to proper sand conditioning and desired feel
mulling and mixing equipment is one of the most critical aspects of sand conditioning, with the manufacturer of the equipment being the best resource for information
the addition of higher levels of Western Bentonite and chemical modifiers will enhance many green sand molding systems (even those systems that are working well but require optimization).
Metalcasters must be able to use all of their tools when judging their sand system. From the feel of the sand to the data from test results, the inexact science of sand conditioning and testing re-quires all senses for success. MC

The only true way of determining acceptable molding sand lies in the quality of the casting it produces. But for efficient production, the sand must be tested before it reaches that point.

Through testing, a foundry that utilizes automatic matchplate molding (shown above) increased its level of Western Bentonite by 20% to achieve the desired sand characteristics.

In the tests, a foundry that employs vertically-parted molding increased its level of Western Bentonite by 10% to improve its sand.
About the Authors
Victor S. LaFay and Stephen L. Neltner have more than 40 years of combined experience at Hill and Griffith Company providing foundries information and analysis related to the green sand molding process and its additives and defects.
For more information:
V.S. LaFay and L. Neltner, “Forget Southern! Go Western with Green Sand Binders,” MODERN CASTING, October 2002, p. 24-26
V.S. LaFay, “Effects of Chemical Surfactants on Clay-Bonded Systems,” MODERN CASTING, 1993 p. 25.
Published in MODERN CASTING / February 2004, Download PDF
Metal Foundry Related News
Comments