Forget Southern! Go Western Bentonite Green Sand Binders
- Hill and Griffith
- Oct 3, 2017
- 7 min read
This article explores the feasibility of using a predominantly Western Bentonite preblend in place of the traditional Southern and Western Bentonite binder makeup.
By using a Western Bentonite - dominated binder, overall bond usage by a foundry can be reduced with an increase in mold hardness.
Some of the questions a foundry would ask about converting to this Western - dominated binder are answered to provide practical guidance to foundries considering a switch.
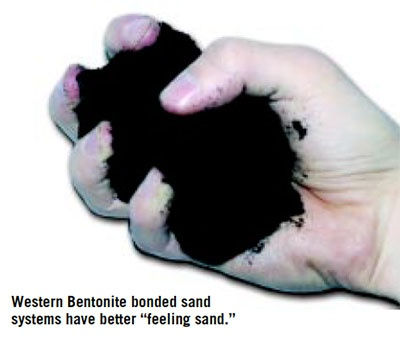
Looking back at green sand molding for the last 30 years, most foundrymen would say that little has changed. Although new molding technology has been developed, to most foundrymen, the general makeup of a green sand mold — sand, water and clay, etc. — hasn’t seemed to change at all.
Well, “most foundrymen” are wrong.
A trend in green sand binders has emerged that has gone relatively unno-ticed. Traditionally, green sand binders have been a blend of Western (Sodium) Bentonite and Southern (Calcium) Bentonite. The new trend is a reduction in the use of Southern Bentonite for preblends, shifting to a predominately Western Bentonite bonded green sand mold.
In order to accomplish this and continue to produce quality molds, the preblends have been modified. These modifications include: the blending of selected carbonaceous additives (pre-dominately causticized lignite and carbonaceous dispersions) into the preblend; the addition of low concentrations of chemical surfactants to the preblend; and the addition of Western Bentonite specifically selected at the mineral site or one specially modified at the manufacturer’s mining facility.
What is most surprising about these new preblend additives/modifications is that they have been available to the foundry industry for years but have only recently received wider acceptance. This acceptance has been due to economics, and foundries’ willingness to “try different techniques” to reduce costs.
What are the benefits to changing to a predominantly Western Bentonite bonded sand system?
One of the primary advantages to a predominately Western Bentonite bonded sand system is economics. Green sand systems that are predomi-nately Western Bentonite bonded usu-ally result in lower bond requirements. The reduction is dependent upon the engineering of the foundry, casting dimensions, molding equipment and many other conditions. A “typical” foundry can experience a bond reduc-tion of 10% with a Western Bentonite bonded sand system.
Another important reason to con-sider predominately Western Bento-nite bonded sand systems is to im-prove casting quality and cleaning costs. Recent casting trials have revealed that these sand systems can have better “feeling sand.” Many foundries rely on the “feel” of a sand system as a function of quality. A parallel to this consideration is the appearance of the sand system. A high quality sand system has a “black silky” appearance (in contrast, if a sand system has a “dull gray” look it is usually a poorly performing system). Both of these positive characteristics can be related to reduced cleaning time for castings and reduced casting defects (usually inclusion-type defects).
Another important consideration with a Western Bentonite bonded sand system is the relationship to high-density molding. A predomi-nantly Western Bentonite bonded sand produces a more dense and “hard” mold on today’s high-pres-sure/density molding lines than the more traditional Western/Southern combination sand.
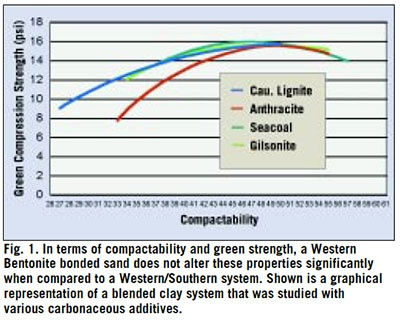
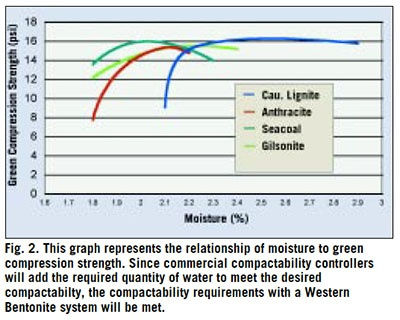
To accommodate predominantly Western Bentonite bonded sand, what changes must a foundry make?
First and probably most important, a foundry must have an efficient mix-ing/mulling operation. Western Ben-tonite has different characteristics than a traditional blend of Western and Southern Bentonite. Failure to recognize these characteristics could be fa-tal to the performance of the green sand molding system. The reason that additives are used is to enhance the performance of Western Bentonite. If the preblend with additives is not prop-erly dispersed throughout the molding sand, then the resultant molds will be less effective compared to traditional molds produced with molding media that isn’t thoroughly mulled.
In terms of compactability and green strength, a Western Bentonite bonded sand does not alter these properties significantly. Figure 1 is a graphical representation of a blended clay sys-tem that was studied with various car-bonaceous additives. However, it is critical to realize that the moisture nec-essary to generate compactabilty could be different with a Western Bentonite bonded sand. Figure 2 represents the relationship of moisture to green com-pression strength. Since commercial compactability controllers will add the required quantity of water to meet the desired compactabilty, the compactability requirements will be met with a Western Bentonite bonded sand, just with differing water requirements.
Another consideration is the “targeted compactability” of the molding sand that is prepared with predomi-nately Western Bentonite bond. When a foundry converts to the new bond system, a change in target compactability usually results. Since the system has been reengineered, it is logical to assume changes in control characteristics also will occur. For example, chemical surfactants prefer green sand systems with higher compactabilities. Also, the other additive materials will prefer compactabilities that may be different than the traditional control characteristics. As a result, upon startup, a new target compactability must be established for each specific operation.
What are the new additives for the preblend for the predominately Western Bentonite bonded sand system?
Selected Carbonaceous Additives (predominately causticized lignite and blended car-bonaceous dispersions) — These materials are widely used in the foundry indus-try for multiple applications and will positively modify the characteristics of Western Bentonite. The materials, added to a preblend at 3-7% based on the weight of the preblend, improve flowability and mold integrity of a sand system.
Low Concentrations of Chemical Surfactants — These materials have re-ceived increased consideration in the foundry industry. As a “rule of thumb,” these additives are added at 3-15 ounces/ton of molding sand. The concentration of the materials is dependent upon the specific manufacturer’s recommendations.


These molds were produced with state-of-the-art high pressure and density green sand molding lines. A predominantly Western Bentonite sand system produces a more dense and hard mold with these molding systems than a Western/Southern blend.
These materials positively modify both Western and Southern Bento-nite. The chemical surfactants can be added to a foundry molding sand either in the preblend or as an indi-vidual ingredient at the foundry (usu-ally at the mulling station). A caution must be observed, however, because overuse or saturation with these ma-terials can result in deteriorating green sand properties.
Western Bentonite Specifically Selected at the Mineral Site or One Specially Modified at the Manufacturer’s Mining Facility — This modification to the preblend can take two forms. First, a specific selection at the mineral sites of a type of Western Bentonite can be used. Second, a Western Bentonite material that has been modified at the manufacturer’s mining facility can be used. These blended clay technologies generally have no limita-tions as to their percentage in a preblend formulation. The selection of the type and quantity is dependent upon specific foundry requirements, the casting design and other considerations.


What are the negative side affects of considering a predominately Western Ben-tonite bonded sand system?
This technology is not for everyone. Certain foundries that have engineering design limitations (mixing/mulling, mold-ing equipment, etc.) may not be able to accommodate the required changes to their production system. Foundries that attempt to modify the preblend to over-come equipment variations in their op-erations will not be successful.
A second concern is that as a bond reduction is realized within a sand sys-tem, it is important to maintain the re-quired combustible levels. Since the design of this preblend is to reduce the bond consumption level (binder), the need to maintain a desired combustible level must be determined. Some of the modifying materials in the new preblend are carbonaceous based and contribute to the combustibles, but in many preblend formulations the quantity of seacoal or seacoal supplements require review. The need to have a desired “casting peel” will depend upon the quantity or type of carbonaceous additives.
As many foundries have discovered, when a change is made to one element of a sand system it usually has an affect on other elements. Foundries that have not reviewed the required carbonaceous additives in the molding sand have not had as successful a conversion to the predominantly Western Bentonite system.
A third consideration is the casting mix produced in a foundry, which affects the type of preblend used for the green sand. Some foundries have certain casting characteristics met by Southern Bentonite. For example, Southern Bentonite develops green compression strength differently than Western Bentonite. Southern Bentonite also lowers hot compression strength, which reduces stress crack defects. Southern Bentonite also helps to improve a green sand mold’s shakeout performance.
The last consideration is the higher cost of a Western Bentonite preblend. As a “rule of thumb,” a preblend that contains predominately Western Bentonite is more expensive. However, in practice, the reduction in bond usage and casting defects offsets this cost increase and results in a cost savings.
What to Do?
The conversion to a predominately Western Bentonite bonded sand system can result in savings for a foundry. The cost of the preblend or separate ingredients will result in an increased up-front cost, but will reduce the over-all production costs of the foundry through both bond usage reduction and reduced casting defects.
To determine if the switch to a Western Bentonite - based system is right for your foundry, perform an analysis with a sand additive supplier. With the pressure on today’s U.S. foundry industry to reduce all costs to be competitive in a global market, no sand grain can be left unturned.
About the Authors
Victor S. LaFay and Stephen L. Neltner have more than 40 years of combined experience at Hill & Griffith providing foundries information and analysis related to the green sand molding process and its additives and defects.
For more information:
Visit www.moderncasting.com to view “Evaluating Emission Characteristics of Seacoal and Seacoal Supplements Using Advanced Analytical Techniques,” LaFay, Neltner, Taulbee, and Wellbrock, 2000 AFS Transactions (00-46), AFS, Des Plaines, IL (2000) and “Effects of Chemical Surfactants on Clay - Bonded Systems,” V. LaFay, Modern Casting, March 1993 p. 25. Green Sand Additives, 2nd Edition, AFS, Des Plaines, IL (2001). “Evaluation of Green Sand Properties and Clay Behavior at 7 to 15% Bentonite Levels,” Shih Green and H. Heine, 1984 AFS Transactions (84-68), AFS, Des Plaines, IL (1984).
Published in MODERN CASTING / October 2002, Download PDF
Comentários