NADCA Video News Update: Die Casting Defects - Surface Defects Part I

There is not one single person that is responsible for die casting surface defect prevention. Everyone must participate. It’s not just the die casting tool room, die cast part designer, die casting machine operator, die casting machine set-up person, die casting inspector, etc. Anybody that is adding some value and designing the overall part has a role when it comes to minimizing defects.
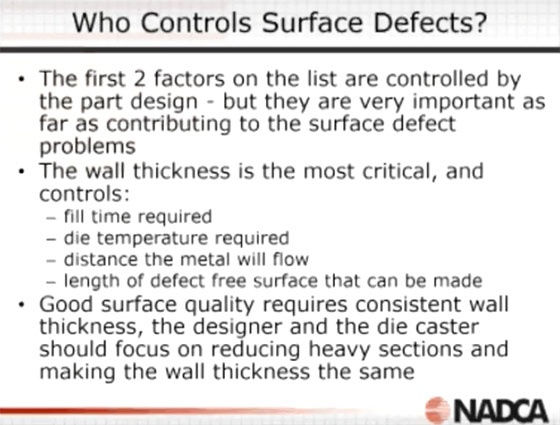
The first two factors on the list, the wall thickness and the overall casting shape, are controlled by the part design - but they are very important as far as contributing to the surface defect problems. The wall thickness is the most critical, and controls:
Fill time required
Die temperature required
Distance the metal will flow
Length of defect free surface that can be made when we cast the part
Good surface quality requires consistent wall thickness. Die casting likes uniform wall thickness. The designer and the die caster should focus on reducing heavy sections and making the wall thickness similar or the same as possible throughout the entire geometry. I recognize that can be a very difficult problems with highly complex castings but when we see things like “metal savers” or ribs and things of that nature. That intent may have been not just and intent to save metal but to make a more die casting friendly part by trying to add uniform wall thickness. The material presented in this video are some highlights from NADCA’s online webinar - Energy in Die Casting - presented by NADCA's Steve Udvardy. This course opens with defect tracking and then discusses various factors that can contribute to poor surface conditions. Click here for information. For information on purchasing a downloadable copy of this webinar in its entirety, please visit: www.diecasting.org/store/detail.aspx?id=WEB293

(Image from the North American Die Casting Association's "EC-515 Die Casting Defects" course by Dr. Steve Midson.)
Comments