Die Casting Porosity Causes and Solutions - Part 2
- Hill and Griffith
- Apr 18, 2018
- 4 min read
By Tim Cowell, Hill and Griffith Company, Technical Director
Gas Porosity (Runners)
The next location of trapped air is likely to be in the runners. Any sharp corners, high or low ejector pins, or small to large area changes in the metal flow path in the runner system will cause air entrapment. The main rule is that the runner has smooth, rounded corners, that it has ever decreasing area from the plunger to the gate, and that the ejector pins be flush. How much problem will a low ejector pin cause? It is very likely that it will not be noticeable on any given casting, but there is absolutely no question that it adds porosity to the casting somewhere, it is just a question of whether it is a quality issue for this particular casting.
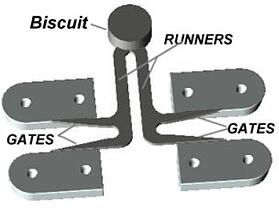
Sometimes an x-ray of the casting with the runner in place will show the bubbles coming from a trapped air location.

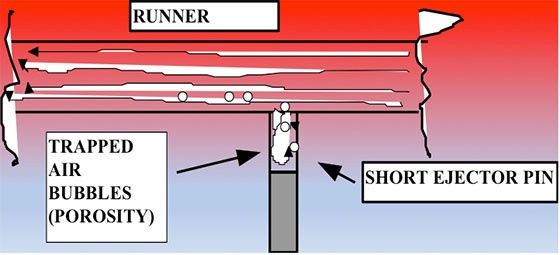
Effect of short ejector pins.

Once the metal starts to enter the cavity, it will normally flow at a high velocity, and will be transformed to atomized flow. This is a very turbulent flow condition, and will trap some of the air present as gas porosity. Again, it would be desirable to use slow and non-turbulent flow to minimize this problem - but this type of flow will not fill the typical die casting.
Gas Porosity (Cavity)
The flow pattern design should be such that the metal tends to push the air through the cavity to the vents. Much of the air in the shot sleeve and the cavity can be pushed out the vents or the vacuum system if these systems are designed correctly. One way to size the vents is to assume that the flow rate of the air leaving the cavity must be equal to the metal flow rate entering the cavity - then set the desired maximum air velocity at about 70% of the speed of sound (to keep back pressure from building up).
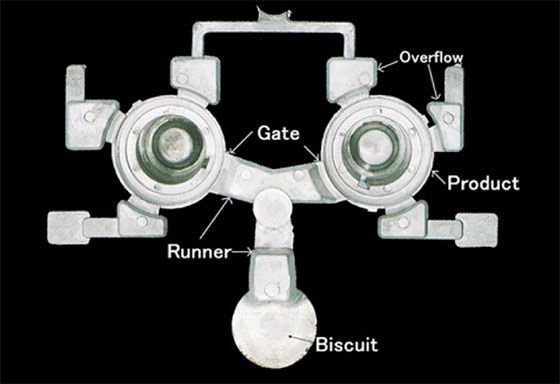
Gas Porosity – Key Check Points To summarize, the control of trapped air porosity will involve a check list like the following: Plunger control settings
Pour rate
Delay before shooting
Pour hole speed
Start slow shot point
Slow shot speed
Fast shot start point
Runner area
Square corners
Low or high ejector pins
Increasing runner area in the metal flow path
Cavity
Vent at location at last place to fill
Vents sized right and go to edge of die
Vents need to be kept clean
Gas Porosity (Steam)
Steam comes from water on the cavity surface when the metal arrives. The water explodes into steam, with the steam occupying a space about 1700 times the space of the original water drop. Thus a very small amount of water will make a very large amount of gas (steam). This gas is mostly trapped in the metal because there is little chance to push the gas out the vents - the gas is not present until the metal arrives, and so is mixed with the turbulent metal flow as soon as it is generated.

The water is mostly from the die spray (which is about 99% water), but it can also be from other sources. Some of the water will evaporate from a hot die, but you cannot count on this happening. Therefore, it is critical that the die be dry when it is closed.
Other sources of water on the die:
Leaking water lines
Dripping overhead sprayers
Leaking hydraulic cylinders

The leaking water lines may be hard to catch - if it is a crack or a poor threaded connection it may only open when the die is locked and under pressure - you may have to close the die, not shoot, then open again and look for moisture. Steam porosity tends to be either a few large bubbles or a group of smaller bubbles. The bubbles are probably white or even a little shiny. If it is from a water line leak, the bubbles may always congregate in about the same location.

Gas Porosity from Steam - Key checkpoints
Checklist to reduce gas porosity from steam:
Too much water based die lubricants on the die (the die must be dry as it closes)
Leaking water lines
Leaking water pipe connections
Crack in the die into a water line
Sprayer dripping on the die as it closes
Water glycol hydraulic fluid getting on the die
What is die casting plunger lubricant? High pressure die casting is a manufacturing process in which molten metal is injected, with a die casting machine using high pressure into a steel die to form various products. Motion metal is first placed into a holding cylinder, a plunger closes off the opening and then forces the metal into the die. Plunger lube provides the necessary lubricating functions for the holding cylinder sleeve, plunger and plunger tip. The plunger lubricant is easily applied to the plunger tip with a swab, brush, or lube dispenser. The lubricant is not conducive to spraying unless pre-heated.
Die Casting Process in Google and NADCA News:
Comments