Concrete Form Seasoning and Material Selection
- Hill and Griffith
- Jun 29, 2017
- 8 min read
Which concrete form substrates and finishes are best for your application?
Considering what form substrate what form substrate material and what surface finish will be best for an application depends on the surface finish specified for the concrete, the number of form reuses the project requires, the strength and deflection characteristics of the substrate, price, and perhaps the thickness tolerances of a product—especially important for architectural concrete work.
Choices for form substrates and surface finishes range from inexpensive CDX plywood that serves as both the substrate and the surface finish, to more expensive aluminum, steel, or plastic resin composite materials with exotic finished surfaces for multiple reuses. The latter may be the bargain compared to plywood when considering the per placement cost versus the original purchase cost. Which substrate and surface finish to use is driven by project requirements. If the forms will be reused 100 times, form panels should be purchased to meet the requirement. Refacing a form assembly halfway through a project causes delays and is expensive. Conversely, it isn't cost productive to invest in materials that can get 100 uses for a job that will only require 20.

(Image from Wharton Concrete Forms.)
This article was published on Nov 25, 2008 in CONCRETE CONSTRUCTION Magazine by Marcus Chase
Concrete Form Substrate Materials
Plywood, steel, aluminum, and composite materials are used for both vertical and horizontal forming systems as a substrate material. Located behind these panels are an array of strong-backs, whalers, and trusses that also are made from wood, steel, or aluminum. There are many substrate material and surface surface finish choices choices in the marketplace, each each with advantages with advantages, disadvantages, and costs. The challenge is to select the right product for the product the job.
Wood substrates
For single-use applications, CDX plywood is probably the cheapest substrate material when the concrete finish doesn't matter. For example, the back side of a unique retaining wall section not in public view might be a good application for a single-use form. But be aware that CDX is designed for other purposes, has only 5 plys, and isn't rated for the pressures that concrete can impose. For repetitive work, better grades of plywood are necessary. They don't absorb as much moisture and help to reduce the concrete build up (laitance build) on the casting surface. These can be pre-oiled panels or substrate plywood panels with waterproof surface finishes. Most plywood for concrete forming is 7 ply, though there is some plywood available with more laminations. Although some 5-ply sheets are available, most contractors prefer 7 ply because they are stronger and have less deflection. Sheets are manufactured by either a one-or two-step process. Manufacturing a one-step sheet involves placing the overlay material and all the veneers with waterproof and boil proof glue in a hot press. The resulting panel has thickness tolerances of ± 1/32 inch. Two-step panel processing involves gluing the veneers in a press, repairing panel faces with poly-patch compounds, sanding the surfaces smooth to a tight tolerance, and then bonding the overlay surface to the panel in a hot press. These panels have thickness tolerances of ± 0.005 to 0.006 inch with no transfer of grain lines or knot holes to the concrete, making them a good choice for high-end, architectural concrete finishes. The first place deterioration starts on a wood panel is along the edges because water can easily enter and cause swelling. Manufacturers of overlay panels typically seal the edges with polymer products so every cut you make also should be sealed. Here are some of the wood substrate classifications available.
B-face
B-back, oiled, and edge sealed (BBOES). Plywood panel surfaces are ranked as “A,” “B,” or “C.” Surfaces marked as “B” permit 20 to 25 knot holes and exposed grain on a 4x8-foot sheet. “Oiled” refers to the panel being oiled during the manufacturing process to allow for easier release from the concrete. “Edge sealed” means the panel edges are sealed at the factory to reduce moisture absorption. BBOES is typically made from either Southern Yellow Pine (SYP) or Douglas Fir (DF). SYP panels are less expensive than DF and usually are heavier. DF panels typically are better quality than SYP because moisture doesn't cause them to swell or move as much and they are almost always the panels used for overlay surfaces. All BBOES products will exhibit grain and patch transfer to the finished concrete. You can expect four to eight uses and the application of release agents is required before each concrete placement.
Hardwood panels
Hardwood veneers on top of DF panels offer blemish-free surfaces with less moisture absorption. The wood for these veneers includes maple, oak, Brazilian, and Indonesian hardwoods. Used as overlay panels, they are cleaner and offer better adhesion for overlay resins.
Steel substrates
The typical substrate thickness of a steel panel is 3/16 to ¼ inch, but can be as little as 14 gauge for handset panels. With a life expectancy of several decades, or even a lifetime, deflection of these panels is minimal and create very smooth concrete surfaces. When using steel forms, designers usually are concerned more about panel joint and tie-hole locations than finish. Steel deck forms feature a steel frame, a plywood substrate, and a resin surface finish. Form manufacturers generally require thin-film, reactive-type form release compounds for good form release.
Aluminum substrates
Like steel, the aluminum in a panel serves as both the substrate and the finished surface. Standard substrate thicknesses range from 0.094 to 0.120 inch, but they can be more for gang form wall panels where greater head pressures are anticipated. The panels are much lighter than steel, are built to have little deflection under load, and can provide very smooth concrete finishes. When they are properly cared for, you can achieve more than 2000 uses. New forms must be “seasoned” (some manufacturers preseason them) to avoid a reaction between the aluminum and the alkali of the cement that results in a disfigured surface.
Overlay finishes
Material that is factory applied to any given substrate is referred to as an overlay. Overlay panels are alkali resistant and minimize labor costs by reducing clean up time between placements. They are more resistant to moisture penetration—increasing resistance to cracking or “checking” as well—extending the life of the form. They also produce smooth concrete finishes. There are two categories of form surfaces with a resin impregnated paper: medium-density overlays (MDO) and high-density overlays (HDO). MDOs consist of a large family of phenolic resin impregnated overlays designed for use on engineered wood substrates. Easy field use combined with the ability to produce superior matt or architectural finishes make them a favorite choice for concrete contractors.
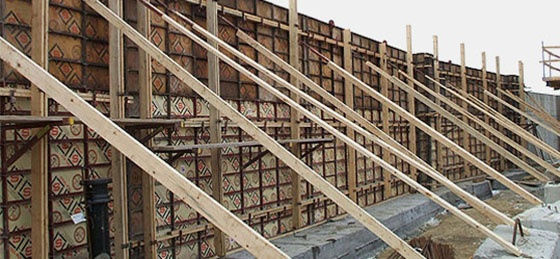
(Image from Wharton Concrete Forms.)
MDO panels
MDO 1 step panels incorporate a layer of Kraft brown resin impregnated paper. The concrete surfaces produced by them are smooth with some grain and patch transfer. You typically can expect eight to 12 placements. MDO 2 step panels provide a smoother finish. Surface blemishes in the base panel are repaired and sanded before the resin impregnated Kraft paper is added. The result is a smooth matt finish that can handle 12 to 15 concrete placements.
HDO panels
HDO form surfaces are especially good for high-gloss architectural finishes. Like MDOs, they encapsulate paper in resin, but the resin content in HDOs is higher—varying from 48% to 58%. There are two types of HDO.
HDO 1 Side 1 Step
Paper and resin is placed on both sides of an engineered panel to minimize moisture penetration, thereby helping panels to stay flatter or balance the sheet. The expected usage is 20 to 35 concrete placements.
HDO 2 Side 2 Step
Substrates are first glued, patched, and sanded to close even thickness tolerances. Then 48% to 58% resin impregnated paper is bonded to both sides.
Melamine overlays
The least expensive version is a very thin melamine layer over particle board for limited-use application. The more durable version features 2-mil build ups that add both weight and expense to a form. But the number of reuses makes it worth the cost and finishes are architectural grade.
Composite resin systems
These create perhaps the best overlay system of all—the only ones that can be applied over a metal surface. They are made with polyethylene and polypropylene, or mixtures of plastic materials. Nail holes and dents can be easily repaired. They are more expensive to purchase but with proper care and maintenance are reusable as many as 100 times.
Composite systems
One substrate panel is built with foamed polypropylene sandwiched between thin sheets of aluminum or fiberglass with polypropylene surface finishes. Because there is no wood in the system, cleaning can be achieved in less time by using a pressure washer and 1000 reuses are possible.
Urethanes
Urethane creates a hard, durable finish and concrete contractors sometimes apply them over inexpensive forms. But considering the cost of the material and labor to apply, this approach is perhaps not worth it.
Concrete form releases
All surface finish products require the use of form release products and all forms manufacturers stress the need to use minimal amounts that won't affect surfaces adversely. Excessive amounts of release agents can cause a vacuum or sticking affect on some denser surfaces. Most of the recommended products react with the alkalinity of concrete to produce soapy films that break the bond between forms and concrete.
Choosing a system
Contractors sometimes make the mistake of choosing a form panel system based on initial cost. If they know they will need to reuse their panels 80 times on a project and choose a product that will only get 60 reuses, they will have to remove the panels from their form system and replace them in order to complete the job—this adds labor, job downtime, and new panel costs. There is a cost advantage to choosing a system that will complete all the placements. Calculate the total uses for a project and buy in order to complete the entire job with one purchase. Marcus M. Chase is senior vice president of market development and sales for MAXAM Industries Inc. He brings nearly 22 years of experience, with a special focus on wood and the concrete forming industry. He has either developed or assisted in development of new concrete forming panel technologies in high reuse, no oil, and LEED-compliant materials. Joe Nasvik is a senior editor for CONCRETE CONSTRUCTION magazine.
Forest Stewardship Council (FCS)
You may see a specification for FSC panels. This refers to how the lumber was grown, farmed, or cut from native stands. In order to produce FSC panels, the manufacturer of the forms must be certified as well as the logging enterprise and all parties in the transaction. This is referred to as the “chain of custody.” Only a handful of mills are certified at this point but you will undoubtedly see more specifications for FSC products.
Tips on how to maintain forms
Every time you cut a panel be sure to apply edge seal over the new cut.
When you stack form sheets, stack them face to face.
Don't expose form surfaces to the sun for long periods of time.
Use a good form release product and apply it sparingly before each concrete placement.
Clean form surfaces shortly after removing them after a concrete placement.
Repair nail fastener holes and dents as they occur (few contractors do this).
Grifcote CC-150-VOC is widely used for concrete form seasoning for optimal concrete release.
Spraying form release agents on mixers and equipment reduces labor and cleanup at the end of the day eliminating concrete adhering to the equipment.
The Hill and Griffith Company also works closely with pipe and form equipment manufactures to provide optimum concrete release characteristics with their equipment.
All Grifcote products are readily biodegradable, which means they have a half-life of 28 days or fewer. And by definition, all Grifcote products are inherently biodegradable with a half-life of 60 days or fewer.
Comentários