Article Review: Electric Vehicles and the Prospects for Aluminum Casting
- Hill and Griffith
- Jun 5, 2018
- 3 min read
Improving battery technology and pending regulations on internal combustion engines are boosting the outlook for EVs, which means new possibilities — and some risks — for foundries and die casters.
by Jost Gaertner, Foundry Management and Technology | Jun 01, 2018

Electric vehicle (EV) prices are falling faster than predicted, and the consumers’ cost of ownership could reach parity with standard internal-combustion engine (ICE) vehicles in Europe as early as 2018, according to USB. Forecasts for EV sales are being revised upward, as the technology improves, promising longer ranges and shorter charging times in the near future.
Meanwhile, the list of countries imposing regulations (or even bans) on ICE vehicles is growing longer. The Netherlands and India recently announced complete sales bans on ICE vehicles starting in 2025 and 2030, respectively, while China and EU have sales quota systems on the agenda for plug-in electric (PHEVs) and battery electric vehicles (BEVs).
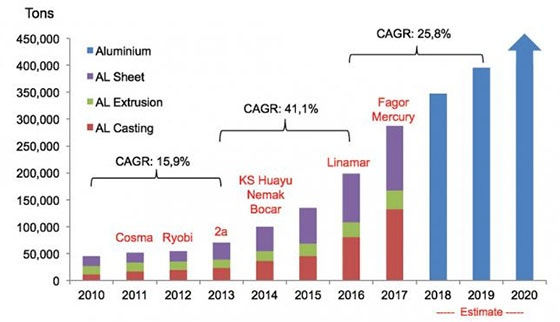
Risk of overcapacity
Currently, lightweight materials like aluminum, magnesium, and carbon fiber are in high demand as lower weight equals longer range, or a reduction of the battery cost for an electric vehicle. But, the fast-developing BEV segment could lead to overcapacity in the aluminum casting industry around 2025-2030.
In particular, foundries and diecasters serving the powertrain segment, together with peripheral components such as pump housings, are in the danger zone. To deal with the additional demand for HEV and PHEV cast aluminum components, metalcasters have added capacity (as likewise have the screw, hose, and pipe manufacturers,) some of which will become redundant as the BEV share increases.
BEV vehicles contain much less cast aluminum in the powertrain compared to ICE, HEV and PHEV vehicles. Engine components like cylinder blocks/heads, oil pans, turbochargers, and manifolds, to list a few, are not needed for battery electric vehicles.
For PHEVs, the difference in aluminum casting powertrain utilization is even higher, considering PHEV applications like electric motors, batteries, and power electronic housings. Should cast aluminum become the preferred solution to house the battery on BEVs, the difference in the cast aluminum utilization would be narrowed considerably. At this time, however, steel or hybrid solutions seem to be preferred by the OEMs.

Increasing structural applications
One may argue that the increasing use of automotive structural aluminum castings will more than offset a possible decline in demand for powertrain applications. Structural aluminum casting applications are being used increasingly in the premium segments for applications such as suspension domes, longitudinal carriers, cross-members, doors/gates, and A-B-C pillars.
But it is questionable if the increasing demand for automotive structural aluminum castings applications will more than offset the falling demand for cast aluminum applications expected due to the increasing penetration of BEV vehicles. So far, there have been only a few samples of automotive structural aluminum casting applications in and below the D-Segment (that is, the EU designation for larger cars like the Mercedes C-Class and BMW 3- and 4-Series.
Furthermore, hybrid body structures are being used increasingly by the premium OEMs rather than full aluminum bodies. Audi’s latest generation A8 D5 (body weight 621 lbs., 58% aluminum) was launched with a hybrid structure that resulted in a heavier body compared to the outgoing A8 D4 (509 lbs., 92% aluminum) structure.
Looking at newly launched BEVs, like the Tesla Model 3, Chevrolet Bolt, and Nissan Leaf, all feature a steel structure. The VW ID will, according to industry sources, become a steel structure with some components made from aluminum and magnesium; and the next generation BMW I3 is said to lose its carbon/aluminum passenger cell/drive module. In fact, BMW and Benteler have de-invested from carbon engagement.
Two-thirds of automotive consumers consider the 300-mile/480-km range on a single charge as sufficient (according to USB.)
Next-generation BEVs from VW, Nissan, Daimler, and BMW are expected to have a range of 500-600 km. Solid-state batteries as announced by Toyota, BMW, and VW will increase the range even further, and bring charging times down to “a few minutes.” If solid-state batteries perform as the OEMs project, when they are launched around 2022, one of the main incentives to use lightweight materials — powertrain efficiency — will no longer fully apply, and demand for automotive aluminum castings could decrease as a result.
The technical commercial conditions are in place. Add to that a potentially global economic downturn, and we could see a painful overcapacity in the aluminum foundry industry.
Jost Gaertner is managing partner of AluMag Automotive GmbH, a market research and development service. Contact him at j.gaertner@alumag.com
Metal Foundry News - From Google and AFS
Comments