8 Die Casting Defects: Root Causes in Processes and Their Remedies
- Hill and Griffith
- Sep 9, 2020
- 4 min read
Excerpt from the March 2017 issue of International Journal of Engineering Research and Application by Vaibhav Ingle and Madhukar Sorte
I. Introduction
Casting is a manufacturing process where hot molten metal is poured into a mold to solidify as a casting. Castings are most often used for making complex shapes that would be otherwise difficult or uneconomical to make by other methods. Casting is a process which carries risk of failure occurrence during all the process to complete the finished product. Hence, action should be taken while manufacturing cast products so that defect-free parts are obtained. During the casting process, there is always a chance where defects will occur. Minor defects can be adjusted easily but high rejected rates could lead to significant change at high cost. Therefore, it is essential for die casters to know and identify the type of defect, the exact root cause, and their remedies. In this review, an attempt has been made to provide all casting related defects with their causes and remedies.
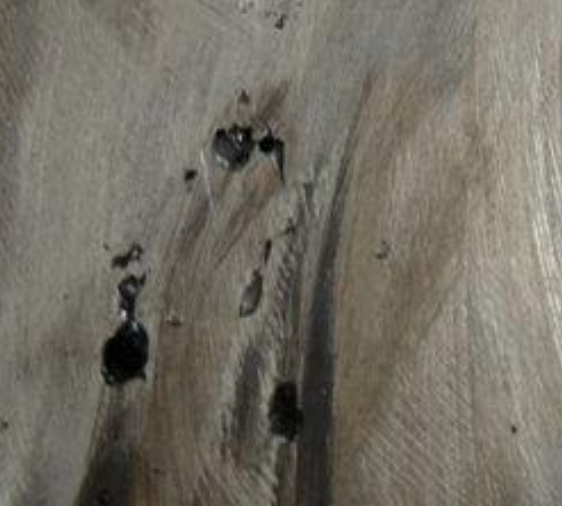
In a casting process, the material is first heated to completely melt and then pour into a mold cavity. As soon as the molten metal is in the mold, it begins to cool. When the temperature drops below the freezing point (melting point) of the material, solidification starts. Solidification involves a change of phase of the material and differs depending on whether the material is a pure element or an alloy. A pure metal solidifies at a constant temperature, which is its melting point (freezing point). An attempt has been made to analyze the critical defects and possible remedial measures are suggested for cast masters to have a sound knowledge about such defects to minimize rejection rates.
II. MOTIVATION
Mostly casting defects are concerned with process parameters. Hence, one has to control the process parameter to achieve zero defect parts. For controlling process parameters one must know the effects of process parameters on casting and their influence on defects. The correct identification of the casting defects at the initial stage is essential for taking remedial actions. Analysis of defects, like shrinkage porosities, through computer aided casting simulation techniques is the most efficient and accurate method. The quality and yield of the casting can be efficiently improved through modifications like the SQC DOE Method simulation technique. Simulations project the shortest possible time and without carrying out the actual trials on the foundry shop floor.
CASTING DEFECTS AND REMEDIES
A properly designed casting, prepared mold and malted metal should result in a defect free casting. However, if proper control is not exercised in the foundry-sometimes it is too expensive casting defect can present themselves. Defects are classified as a filling-related, shape-related, or thermal-related.
4.1 Filling related defects
4.1.1. Blowhole During solidifying, surface of the metal can form a rounded or oval shape hole cavity due to oxidation on smooth or clean surfaces. The oxidation collects into a bubble at the high points of a mold cavity and prevents the liquid metal from filling that space. A blowhole is a type of cavity defect, which can appear as a pinhole or subsurface blowhole. A pinhole is very tiny hole. Subsurface blowholes only can be seen after machining. The defects are nearly always located in the cope part of the mould in poorly vented pockets and undercuts. Read More
4.1.2. Sand inclusion Sand inclusion is nothing but a sand hole or blacking scab, It looks like small or middle holes with sand grain in the internal or on the surface of castings. Inclusion defects looks like there are slag inside of metal castings. Sand inclusions are one of the most common casting defects. This casting defect is formed during abrasion of the mold surface by the metal flowing past and the associated thermo-mechanical stresses. The considerable compressive and shear stresses acting on the mold and core sections can lead to breakage of individual sand grains (erosions) or tearing off of larger mold sections (erosion scabs). This causes interruptions in smooth mold and core surfaces, thickening zones on individual casting sections and sand crusts (sand inclusions) in remote casting areas.
Irregularly formed sand inclusions Irregularly formed sand inclusions are often difficult to diagnose as these defects generally occur at widely varying positions and are therefore very difficult to attribute to a local cause. Read More
4.1.3. Cold lap or cold shut A cold shut is caused when two streams meeting in the mold cavity do not fuse together properly, thus, forming a discontinuity in the casting. When the molten metal is poured into the mold cavity through more-than-one gate, multiple liquid fronts flow together to become one solid. If the flowing metal fronts are too cool, they may not flow together, but will leave a seam in the part. Such a seam is called a cold shut. It is a crack with round edges. Read More
4.1.4. Gas porosity Porosity in castings is due to bubbles being trapped during solidification. The gas can be from trapped air, hydrogen dissolved in aluminum alloys, moisture from water based die lubricants or steam from cracked cooling lines. Gas porosity comes from three main sources in die-casting: trapped air, steam and burned lubricant. Air is present in the cavity before the shot. It can easily be trapped as the metal starts to fill the cavity. The air is then compressed as more and more metal streams into the cavity and the pressure rises. When the cavity is full it becomes dispersed as small spheres of high pressure air. The swirling flow can cause them to become elongated. Read More

4.2 Shape defects
4.2.1. Mismatch defect Mismatch in a mold defect is because of the shifting molding flashes. It will cause the dislocation at the parting line. Read More
Comments